Рождение машины Формулы 1. Часть вторая
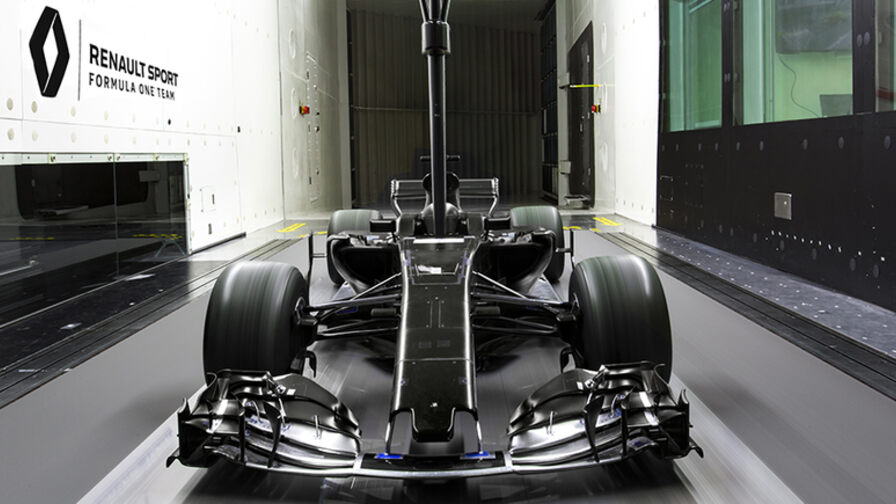
От первых штрихов на чертеже нового шасси Ф1 до его дебюта на предсезонных февральских тестах проходит долгих 12 месяцев. Представляем вам историю производственного зачатия и вынашивания новой машины в двух частях при непосредственной помощи технического директора отдела шасси Renault F1 Ника Честера. Часть вторая, заключительная. Слова автора – Николя Карпентье (F1i.com)...
Окончание. С первой частью можно ознакомиться на нашем сайте.
Двойное ограничение
Когда концепция машины разработана и производственное расписание составлено, инженеры приступают к самой важной и трудоемкой стадии – непосредственному производству 20 тысяч элементов и объединению их в цельную боевую единицу.
Если говорить упрощенно, в процессе разработки немеханических частей (кузов, монокок и так далее) необходимо учитывать два главных аспекта: объем деталей для удовлетворения требованиям аэродинамики и их жесткость для обеспечения прочности общей конструкции.
При этом факторы имеют разное значение в зависимости от того, что это за деталь – внешняя она или внутренняя. К примеру, геометрия переднего антикрыла четко ограничена рамками для оптимизации аэродинамической эффективности, но при этом этот элемент должен обладать достаточной жесткостью. Механические части (амортизаторы, элементы управления, трансмиссия, тормоза) должны быть выполнены с расчетом на конкретную прочность конструкции, но при этом обладать минимальным весом.
Геометрия
Специалисты по аэродинамике используют в своей работе два основных средства: аэродинамическую трубу и вычислительную гидродинамику.
Что касается вычислительной гидродинамики, то ее упрощенно можно сравнить с виртуальной аэродинамической трубой, которая помогает инженерам проанализировать воздушные потоки, обтекающие шасси, еще до непосредственного производства деталей требуемого масштаба.
Тесты в трубе не дают столь же полного визуального эффекта, как средства вычислительной гидродинамики – там речь идет лишь о показателях с нескольких датчиков. Но в плане воплощения в жизнь компьютерных моделей аэродинамическая труба является идеальным дополнением гидродинамике.
В трубе команды испытывают детали и целые модели машин 60-процентного масштаба в различных конфигурациях. При этом они могут моделировать поведение шасси на торможении (со смещением веса вперед) и при прохождении поворотов (с боковыми нагрузками).
Также модель шасси в трубе установлена на платформе, служащей ей дорожным покрытием. Целью специалистов по аэродинамике является создание стабильной нагрузки в широком спектре ситуаций, а не получение максимальной прижимной силы в узком рабочем окне.
Когда объем деталей утвержден, приступают к своим обязанностям инженеры, вооруженные средствами компьютерного дизайна (CAD). Работа здесь ведется в циклическом режиме – макеты постоянно мигрируют из отдела аэродинамики на испытания методом конечных элементов для проверки жесткости и прочности, что при разработке элементов шасси имеет важное значение.
Жесткость
Во время движения любое гоночное шасси подвергается огромному количеству разнонаправленных нагрузок. Монокок, к примеру, принимает на себя силы, действующие на переднюю подвеску, тогда как трансмиссия обрабатывает нагрузки на заднюю подвеску. Что касается крыльев и днища, здесь эти показатели просто зашкаливают.
Как инженеры Ф1 определяют необходимый уровень жесткости деталей? В своей работе они используют два ориентира, помогающих вычислить коэффициент прочности финальной модели. Во-первых, это данные телеметрии с прошлогодней машины. Во-вторых, прописанные в условиях обязательных тестов FIA нагрузки для прохождения омологации.
Для определения требуемого уровня жесткости конструкции инженеры используют упомянутый выше метод конечных элементов, при котором структура делится на конечное количество элементов, которые в дальнейшем подвергаются различным нагрузкам. Наблюдая за результатами, инженеры могут оценить коэффициенты деформации конструкции в сборе. При этом зачастую нагрузки превышают заданные ориентиры, чтобы выявить области, в которых необходимо повысить жесткость.
Этапы разработки
«Вся разработка базируется на прошлогоднем шасси, – отметил технический директор отдела шасси Renault F1 Ник Честер в интервью F1i. – Мы начинаем работу со средств вычислительной гидродинамики, затем переходим к работе в аэродинамической трубе, после чего прототипы деталей проходят испытания на прочность, и только после этого мы отправляем их на производство.
И если антикрыло показывает себя на тестах на прочность и гибкость не лучшим образом, оно отправляется обратно на вычислительную гидродинамику. Иногда мы передаем детали на анализ методом конечных элементов довольно рано, чтобы было время в случае чего изменить геометрию.
Для механических компонентов, для которых не так важна аэродинамика, также необходимо провести процесс оптимизации. К примеру, внутренние крепления элементов задней подвески на коробке передач проходят многократную проверку. Изначально инженеры разрабатывают схему средствами компьютерного моделирования CAD, после чего шаблон отправляется на испытания надежности, по итогам которых принимается решение, нужно ли повысить жесткость компонента или можно ли сделать его легче. Этот цикл может повторяться несколько раз с целью оптимизировать соотношение прочности и веса. И такие итерации происходят применительно ко всем элементам».
Стендовые испытания
Компьютерный анализ жесткости и прочности все же остается компьютерным, то есть виртуальным, и его результаты необходимо подтверждать на динамометрических стендах с максимально приближенной к реальности симуляцией реальных условий.
На базах команд Ф1 есть несколько видов стендов, это и оборудование для испытания подвески, и отдельные стенды для коробки передач и двигателя, и так далее.
Поломка деталей часто происходит из-за их недостаточного размера и невозможности толком провести компьютерное моделирование. Для этого и необходимы стенды, способные показать все отклонения от нормы перед дебютом шасси на трассе.
После того как форма и жесткость всех элементов утверждена, компьютерные чертежи отправляются в производственный цех.
От дизайна к производству
На этом этапе в действие вступают информационные технологии, помогающие трансформировать выверенные компьютерные модели в четкие производственные требования для мастерской.
С использованием средств CAD инженеры получают в свое распоряжение трехмерный мастер-файл с мельчайшими подробностями каждого элемента шасси, включая размеры и особенности сборки.
Являясь, по сути, огромной геометрической базой данных, мастер-файл в дальнейшем передается на оборудование для автоматизации производственных процессов, на выходе которого получается другой файл, содержащий инструкции по программному управлению станками.
Фактически этот файл состоит из четких команд для производственного оборудования по созданию той или иной детали.
Здесь и линии отреза на металлических компонентах, и шаблоны для композитных элементов.
Эти шаблоны в дальнейшем служат для создания карбонового образца, по которому впоследствии производится деталь.
С чего начать?
Если внимательно присмотреться к структуре машины Ф1, становится понятно, что ее "скелет" состоит из трех основных отделов: шасси, включающего в себя монокок, топливный бак и элементы передней подвески, силовой установки и трансмиссии (коробка передач и задняя подвеска).
К этому остову в дальнейшем крепятся элементы кузова, днище, антикрылья, система охлаждения и так далее. Но с чего команды начинают производственную фазу?
«Шасси и коробка передач первыми отправляются на производство, – пояснил Честер. – Следующими идут подвеска и крылья. И в последнюю очередь производятся элементы кузова, в числе которых кожух двигателя. В процессе производства мы оснащаем будущее шасси всей необходимой электрической проводкой.
В ноябре мы обычно получаем готовый тестовый макет. Но помимо компьютерного макета мы также собираем физическую модель шасси. Это лучший способ просчитать расположение проводки вдоль элементов. И хотя эта модель строится на основании компьютерных данных, для схемы прокладки проводов она подходит идеально».
Производство. Ретроспективный процесс
Монокок, элементы кузова и крылья изготавливаются из тонких листов углеволокна, которые обрезаются, формуются и ламинируются в виде шаблона перед отправлением в автоклав. А что представляют из себя эти детали из углеволокна?
Карбон – весьма деликатный материал, и инженеры при работе с ним должны учитывать необходимую толщину слоя и направление волокон. Чтобы избежать ошибок и обеспечить плавность переходов инженеры используют специальное программное обеспечение, позволяющее обеспечить связь между трехмерными моделями и реальным производством.
По сути, это ПО автоматически генерирует инструкции, которые отправляются в цех производства композитных материалов в виде схемы "слой за слоем". Если план разработки меняется, инструкции автоматически обновляются.
Это программное обеспечение способно также заранее выявлять все возможные проблемы при производстве той или иной детали и отправлять инженерам уведомления. К примеру, программа может выявить образование складок углеволокна, исходя из заданных параметров детали. В этом случае специалисты вольны остановить процесс производства и отправить макет на доработку. Это позволяет экономить немало времени и средств.
Производство шаблона
Для карбоновых деталей вроде монокока процесс начинается с создания полноразмерного шаблона. Данные системы компьютерного моделирования отправляются на пятиосевой фрезерный станок, который вырезает шаблон из эпоксидной смолы. Зачастую требуется несколько блоков для производства единой модели.
На базу Renault в Энстоуне недавно поставили новейшее многофункциональное оборудование Breton высотой семь метров, что позволит коллективу своими силами производить объемные компоненты вроде днища шасси и монокока.
К получившейся эпоксидной модели вручную прикладываются слои углеволокна для формирования финального шаблона, который и отправится в автоклав.
Производство деталей
Как только шаблон сделан, начинается процесс производства детали – для этого высококвалифицированные специалисты вручную прокладывают углеволоконные листы вдоль внутренней части шаблона. Лазерная система слежения при этом помогает им не допустить ошибку, помечая на детали кромки и места сгибов (зеленые линии на фотографии выше).
После этого ламинированный шаблон облачается в вакуумную оболочку (все еще внутри шаблона) и помещается в автоклав.
Базы команд Ф1 обычно располагают двумя-тремя автоклавами, где компоненты шасси "выпекаются" в условиях высокой температуры и под высоким давлением.
Для того чтобы повысить прочность композитных структур, они помещаются в автоклав в виде сэндвича. Ячеистое ядро, изготовленное из алюминия или арамида, помещается между двумя композитными слоями, толщина которых варьируется по необходимости.
Места расположения креплений на ячеистом ядре (к примеру, для элементов подвески), дополнительно укрепляются за счет металлических или композитных вставок с целью увеличить площадь приложения силы.
Для сложных деталей, требующих сборки из нескольких компонентов, инженеры применяют технологию адгезионного соединения.
Например, монокок собирается путем связывания воедино верхней и нижней частей после установки двух внутренних перегородок.
На заключительной стадии проделываются необходимые отверстия для электропроводки и других нужд.
Это также делается при помощи пятиосевого фрезерного станка, точно следуя инструкциям из CAD-файла.
Краш-тесты
Монокок изготавливается с расчетом прохождения обязательных краш-тестов FIA.
Различные омологационные испытания под четким контролем FIA проводятся частично на базе, частично в одном из официальных центров, одобренных федерацией. В Великобритании это Центр ударных воздействий в Крэнфилде и Лаборатория исследования транспорта в Энстоуне. Также есть место проведения тестов в Милане.
«Омологационные испытания мы проходим в Энстоуне и Крэнфилде, – подтвердил Ник. – Статические тесты проводим у себя, а динамические – уже в Крэнфилде».
Сборка и обкатка
После того как все 20 тысяч деталей произведены, необходимо собрать их воедино.
«На финальную сборку шасси после производства всех элементов уходит порядка двух недель, – продолжил Честер. – Разработчики выпускают сборочные чертежи для каждого узла (шасси, подвеска, коробка передач и так далее). На сборку некоторых компонентов – в первую очередь это КПП – уходят все две недели, так что их мы отправляем первыми».
Для того, чтобы проверить функционирование всех составляющих, команда использует так называемые съемочные дни – фактически в этот момент производится обкатка нового шасси.
«Обычно мы впервые проводим обкатку машины именно в съемочный день за пару дней до тестов», – подтвердил технический директор отдела шасси Renault F1.
И пока первое шасси транспортируется в Барселону, на базе собирают второй экземпляр, ориентируясь на дату проведения первой гонки сезона. При этом запчасти производятся для зимних тестов, но в ограниченном количестве, поскольку полностью конфигурация аэродинамики на этот момент еще не утверждена.
С учетом того, что между сезонами проходит всего три месяца, рабочие процессы на базе практически никогда не останавливаются. А по окончании предсезонных тестов инженеры уже начинают думать о новом шасси.
Теперь, надеемся, вам понятно, что испытывают инженеры и механики в боксах, когда гонщик разбивает машину на трассе...
Перевел и адаптировал материал: Александр Гинько